Technische Daten
Obwohl es schon vor 10 Jahren, in der Saison 2014 den ersten Rennwagen mit elektrischem Antrieb gab, hatte man damals noch nicht die nötige Ausrüstung und Schulungen, um dabei mit Hochvolttechnik zu arbeiten. Dieses Mal waren wir vorbereitet. Schon in der 2023er Saison waren die ersten Teammitglieder bei Hochvoltschulungen und haben die groben Züge eines Hochvoltsystems und andere Systeme, die für einen elektrischen Antrieb fundamental verändert werden müssen, wurden bereits im Vorfeld aufgearbeitet.
Auf dem letzten Event 2023, Formula Student Germany, haben wir uns bereits umgeschaut, was andere Teams für Designs in ihren Rennwagen verbaut haben und haben uns Tipps und Tricks eingeholt. Dabei haben wir viele Kontakte geschaffen, die uns über die Saison mehrfach aus der Patsche geholfen haben. Dabei wurde uns auch gesagt, dass ein Umstieg von Verbrenner auf Elektro in einem Jahr nahezu unmöglich wäre und eine Teilnahme an Events unglaublich unwahrscheinlich. Wir wollten es trotzdem versuchen, wobei unser ausgesprochenes Ziel immer war, dass der Wagen einmal aus eigener Kraft fahren sollte.
Trotzdem war viel zu tun, fast jede Unterbaugruppe musste massive Veränderungen machen, um den neuen Antriebsstrang zu integrieren. Dabei haben wir uns dazu entschieden direkt den Sprung auf die maximal erlaubte Systemspannung von 600V und Radnabenmotoren zu wagen, wobei wir uns auf einen Hinterradantrieb und Rundzellen beschränkt haben. Wir wollten gleichzeitig so viel wie möglich von den Verbrennern der letzten Jahre übernehmen und so viel, wie möglich bereits für einen möglichen Allrad in den nächsten Jahren vorbereiten. Im Januar haben wir uns dann für die Rennen in Tschechien und Deutschland qualifiziert, die direkt nacheinander stattfanden.
Nach vielen schlaflosen Nächten, viel Arbeit und mit mehr einer Notlösung konnten wir dann im Juli eine erste Fahrt mit unserem RS-24e machen. Damit hatten wir alles erreicht, was wir uns vorgenommen hatten, und wir hatten alle Voraussetzungen erfüllt, um an den Events teilzunehmen. Alles danach, haben wir uns gesagt, ist Bonus. Wir haben die nächsten Monate damit verbracht diese Notlösungen eine nach der anderen zu ersetzen, bis der Wagen Rennfertig war. Dabei wurden die letzten Batteriezellen am Sonntag vor der Abfahrt verschweißt und Ersatz für die Hohlräder, bei denen ein Fertigungsfehler aufgefallen war, wurde auf der Fahrt zum ersten Event eingesammelt und mit Hilfe eines Ovens des Rennteam Stuttgart im Camp verbaut. Das ganze Team hat auch während den Events durchgängig daran gearbeitet den Wagen vollständig Regelkonform zu machen.
Leider wurden alle Anstrengung durch einen Konstruktionsfehler im Batterie Management System egalisiert. Ohne die Zeit, das Werkzeug und die Teile, um den Fehler auf den Events zu beheben, beschlossen wir trotzdem so viel, wie möglich fertigzustellen, um uns möglichst viel Feedback zu unseren Designentscheidungen einzuholen. Durch die Arbeit, die wir auf den Events durchgeführt haben, haben wir viele unserer Designs überdenken können und haben viele praktikable Designänderungen für die nächste Saison gefunden. Eine letzte Möglichkeit zu glänzen hatten wir auf der Waage, wir waren unter den Top 15 leichtesten Rennwagen auf FSG, und das mit einem Erstjahres E-Wagen. Mit dem überwiegend positiven Feedback und den Tipps der Officials und anderer Teams hoffen wir im nächsten Jahr einen weiteren großen Schritt im Design unseres Rennwagens zu machen.
Formula Student Germany
Business Plan Presentation Platz 72 Cost Analysis Platz 63 Engineering Design Platz 56 Gesamt Platz 75 Formula Student Czech
Business Plan Presentation Platz 36 Cost Analysis Platz 43 Engineering Design Platz 36 Gesamt Platz 38
Events
Akku/Elektrik
Durch einen neuen Antriebsstrang stand auch die Baugruppe Elektrik vor sehr großen Aufgaben, wie der Entwicklung eines Akkus inklusive Akku Management System, einer Statusleuchte aus Logikbausteinen und einem neuen Steuergeräts für die Ansteuerung von Invertern und Akku. Dabei hat sich die Arbeit der vorherigen Seasons bezahlt gemacht, weil wir mit einem funktionierenden Controller und CAN-Bus Aufbau in die Entwicklung starten konnten.
Jedes Zellpaket besteht aus 36 Zellen, die durch vernickelte Busbars mit einander verbunden werden. In jedem Block ist eine Platine integriert. Das Akku Management System basiert auf dem Texas Instruments BQ79616-Q1 Chip, der die Spannung und Temperaturen der Akkuzellen überwacht.
Der gesamte Akku besteht aus 12 baugleichen Zellpaketen, dadurch ergibt sich eine Zellkonfiguration von etwa 30 kg in 144 Zellen in Reihe und 3 parallel geschalteten Zellen. Diese Blöcke werden in einem Aluminium Kasten montiert, der die Zellen im Fall eines Crashs schützen soll. Dafür muss der Akkukasten eine Beschleunigung von 20 g in vertikaler und 40 g in horizontaler Richtung aushalten. In den Akkukasten sind mehrere Controller integriert, die die Überwachung der Zellen und Isolation des Systems übernehmen.
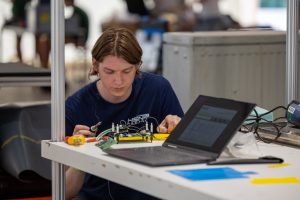
©FSG Lodholz
Antriebsstrang
Seit inzwischen 10 Jahren fahren wir erfolgreich einen Verbrennermotor. Jetzt ist auch für uns die Zeit gekommen, ein neues Kapitel anzufangen –
Mit der Integration eines elektrischen Antriebsstrangs haben wir direkt einen größeren Sprung gewagt und haben uns entschieden, die Motoren in den Radträgern direkt zu integrieren. Dieses Konzept bringt sowohl viele Vorteile als auch große Herausforderungen. Um die Menge an Entwicklungsarbeit zu begrenzen haben wir mit einer existierenden Lösung aus der Formula Student gearbeitet, einem Racing Kit von der Firma AMK Motion. Sowohl Kühlung als auch Firewall mussten vollständig an das neue Konzept angepasst werden. Trotzdem haben wir uns getraut, die Bauteile der Inverter neu anzuordnen, dass sowohl Gewicht als auch Größe deutlich optimiert werden konnten.
Durch einen neuen Antriebsstrang stand auch die Baugruppe Elektrik vor sehr großen Aufgaben, wie der Entwicklung eines Akkus inklusive Akku Management System, einer Statusleuchte aus Logikbausteinen und einem neuen Steuergeräts für die Ansteuerung von Invertern und Akku. Dabei hat sich die Arbeit der vorherigen Seasons bezahlt gemacht, weil wir mit einem funktionierenden Controller und CAN-Bus Aufbau in die Entwicklung starten konnten.
Während der Season hat sich herausgestellt, dass ein gekauftes Akku Management System keine sinnvolle Form für die Anordnung unserer Zellen hat, weshalb wir uns entschieden haben, hier auf eine selbst entwickelte Lösung zu setzen. Das Resultat ist ein sehr kompaktes und praktisches Zellpaket.
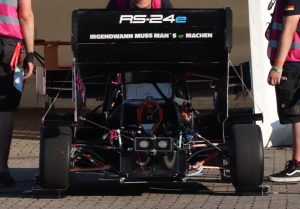
Rahmen
Auch diese Saison bildet ein Stahlgitterrohrrahmen die Basis des Rennwagens. Als Stahl verwenden wir E355, einen unlegierten Baustahl mit guten Schweißeigenschaften. Besonders belastete Rohre wie die Überrollbügel und die Shoulder Harness Bar sind aus 25CrMo5 einem legierten Vergütungsstahl.
Durch den Umstieg auf E-Antrieb haben wir uns auf Änderungen im hinteren Teil des Fahrzeugs fokussiert und im vorderen Teil das bewährte Konzept aus dem Vorjahr übernommen. Um Platz für den Akku zu schaffen und diesen zügig durch das Fahrzeugheck ausbauen zu können wurde die Fahwerkskinematik überarbeitet und die neuen Fahrwerkspunkte in den Rahmen integriert. Desweitern konnten wir einige Knotenpunkte reduzieren, um Gewicht zu sparen. Der diesjährige Rahmen wiegt 30 kg, somit konnten wir 4 kg im Vergleich zum letzten Rahmen sparen.
In enger Zusammenarbeit mit der Aerodynamik haben wir uns überlegt, wie wir die Performance des Wagens steigern können. Wir sind auf die Idee gekommen, den Mainhoop unterhalb der Schultern des Fahrers stark nach innen zu biegen, um Platz für größere Seitendiffusoren zu schaffen.
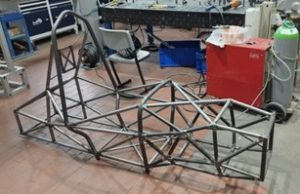
Fahrwerk
Das Fahrwerk des RS-24e wurde durch den Wechsel auf Elektromotoren vollständig neu konzipiert. Dabei lag der Fokus auf der Entwicklung einer neuen Fahrwerksgeometrie sowie der Konstruktion der Planetengetriebe.
So wurde die Kinematik der Hinterachse, durch eine verändert Dämpferposition und der Positionierung der Motoren in der Radnabe, stark verändert. Des Weiteren wurde die Stabilität der Aufhängung aufgrund des neuen Antriebskonzeptes und des Gewichts optimiert.
Das eigens entwickelte Planetengetriebe ermöglicht es, die Elektromotoren nahezu vollständig in der Felge zu integrieren, was die Aerodynamik des Fahrzeugs verbessert, und weitere Vorteile mit sich bringt. Ein Großteil der im Fahrwerk verbauten Komponenten wurde in eigener Fertigung hergestellt.
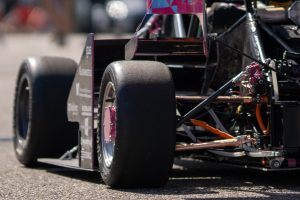
©FSG Seizinger
Aerodynmaik
Die Aerodynamik des RS-24E wurde konsequent weiterentwickelt und basiert auf den Erfahrungen des Vorjahresmodells. Mit der Entwicklung unseres ersten Elektrik-Fahrzeugs (HV-EV) konnten wir den Rahmen gezielt an die aerodynamischen Anforderungen anpassen. Dies ermöglichte die Integration eines breiteren Diffusors sowie die Implementierung einer überarbeiteten Heckgeometrie.
Durch die Anhebung des Front-Bulkheads wurde ein größerer volumenstrom zum Diffusor realisiert, wodurch die Effizienz des Unterbodens gesteigert werden konnte. Ergänzt wurde dies durch neu designte Endplatten, die den aerodynamischen Feinschliff optimieren.
Das Ergebnis dieser Verbesserungen: ein höherer Abtrieb und eine ausgewogene Fahrzeugbalance – perfekt für maximale Performance auf der Rennstrecke.
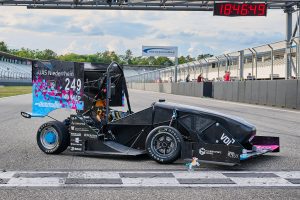
©FSG Grobe